Projection welding: Precise joining technology
What is projection welding and how does it work?
Projection welding is a specialized resistance welding process that is characterized by its high precision and efficiency. This process is mainly used in metal processing to join metal parts, especially sheet metal, securely and permanently. In projection welding, projections or elevations are stamped onto the components to serve as welding points. These protrusions melt under the effect of electric current and pressure, causing the components to be firmly welded together.
The projection welding process begins by placing the workpieces between two electrodes. The electrodes exert pressure on the workpiece and conduct the current. The projections increase the electrical resistance at these points, which leads to localized heating. The projection melts and bonds with the opposite workpiece. As soon as the weld seam has solidified, a firm and permanent connection is created. The entire process takes just a few seconds and can be highly automated.
Technological requirements in projection welding
Projection welding requires special equipment and expertise to achieve the desired results. Modern welding systems enable precise control of the welding parameters, ensuring consistently high quality. For companies involved in metal processing, projection welding offers an efficient solution for mass production as well as for demanding projects with complex geometries.
Visual features of a projection welding system
- Robust and stable construction: The machines are often large and solid to ensure stability during welding.
- Copper electrodes: The electrodes are often clearly visible and identifiable by their copper color.
- Hydraulic or pneumatic cylinders: These are often mounted on the top of the machine and control the pressure on the electrodes.
- Cooling water hoses: These hoses often run along the electrode arms to ensure continuous cooling.
- Control panel: A digital panel with displays and buttons to control the welding process.
Types of projection welding
There are different types of projection welding, allowing a high degree of flexibility and adaptability of the process to different materials and application requirements. Depending on the workpiece geometry, material and required joint strength, the appropriate method can be selected to achieve optimum welding results. This diversity makes projection welding an indispensable technique in many industrial applications.
1. Projection welding with embossed projections
This is the most common form of projection welding, in which the projections are already embossed or formed on one of the workpieces in advance. This method is often used in the automotive industry to join car body parts. The pre-formed projections ensure that the electric current and welding heat are concentrated exactly where they are needed.
2. Projection welding with resistance spots
This is a variant in which the projections are not mechanically pre-formed but are created by the arrangement of the electrodes and the control of the welding current during the process. This method is often used for thinner materials or special components where mechanical pre-forming of the projections is difficult.
3. Multiple projection welding
In multiple projection welding, several projections are welded simultaneously. This requires special electrode systems that ensure an even distribution of current to all projections. This method is particularly efficient when many joints need to be produced simultaneously, such as in the series production of automotive parts or household appliances.
4. Projected projection welding
In projected projection welding, the projections or welding spots are positioned by a special design of the tool or electrodes. This technique is often used for complex or irregularly shaped workpieces where conventional pre-formed projections are impractical. This allows specific points or edges of the workpieces to be welded together.
5. Weld riveting
Weld riveting is a variant of projection welding in which a small rivet-like projection is welded onto a workpiece. This “rivet” is deformed under pressure and heat to create a permanent joint. This technique is often used when thicker materials or different types of materials need to be joined.
6. Projection welding of plastics
Although projection welding is traditionally used for metals, there are also variants for plastics. In this process, special projections are formed on plastic parts, which are then fused together using a thermal method. This technique is often used in the manufacture of plastic housings or components where a strong and watertight joint is required.
Typical areas of application for projection welding
Projection welding is used in many branches of industry, particularly in the automotive industry, where it is used to join body parts, seat structures and other components. The process is also widely used in the production of household appliances, in mechanical engineering and in aerospace technology.
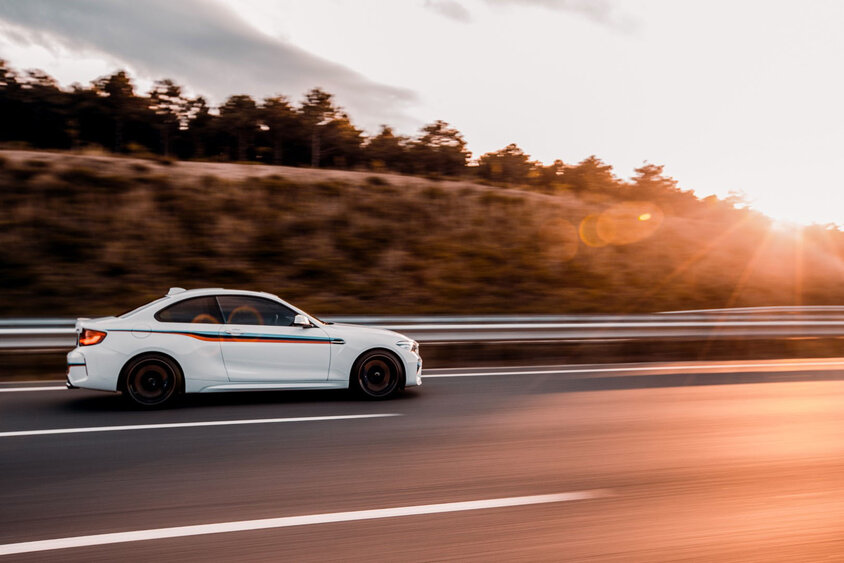
Automotive Industry
Body parts such as door frames, hoods and frame components are often projection welded to ensure stable joints.
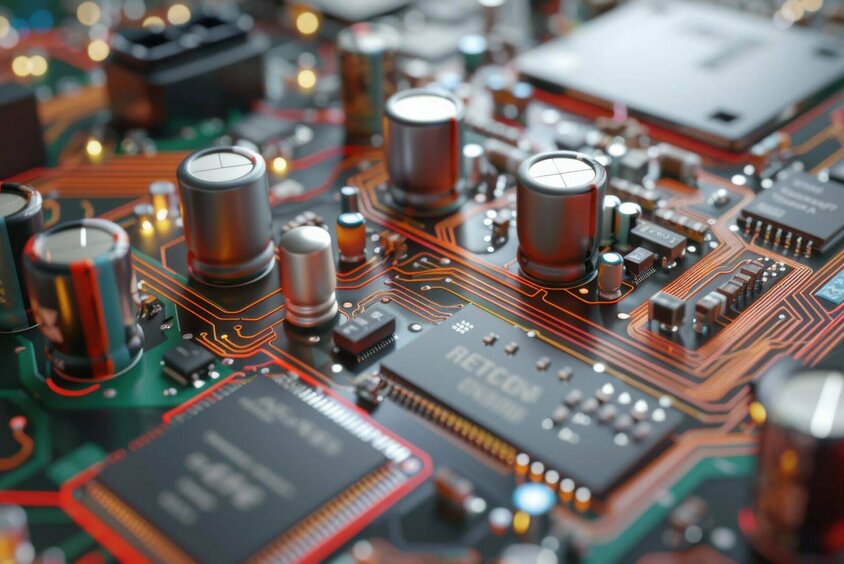
Electrical engineering
Contacts and connections in electrical devices, such as battery terminals, are often produced by projection welding.
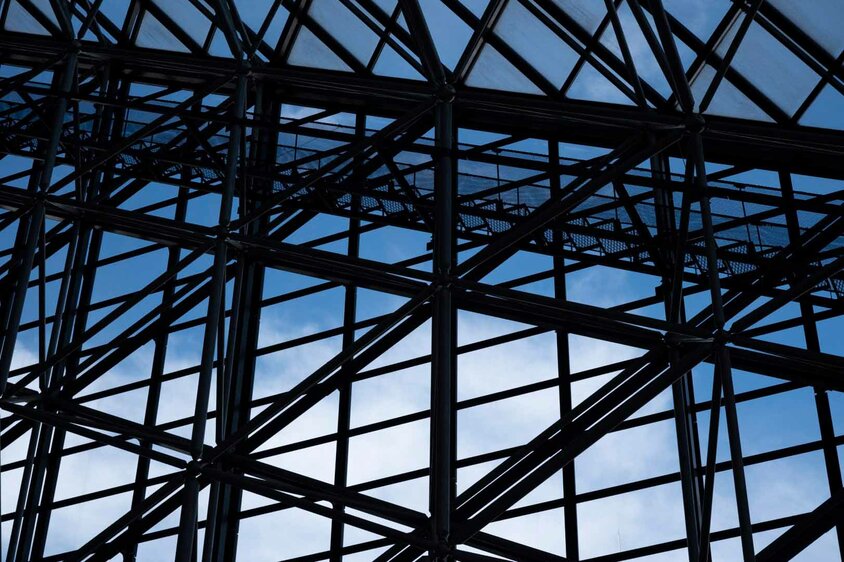
Building Industry
Steel structures and beams are sometimes projection welded to create stable and resilient connections.

Household appliances
In appliances such as washing machines or dishwashers, projection welding is used to permanently join different metal parts together.
The most important parameters for projection welding
In projection welding, several parameters play a decisive role in ensuring the quality and effectiveness of the welding process. These parameters influence the strength, reliability, and consistency of the welded joints. Knowledge and precise control of these parameters are crucial for achieving high-quality and reliable joints in projection welding. By adjusting these parameters correctly, welding defects can be avoided, and consistent quality in production can be ensured.
Overview of projection welding parameters
1. Welding current
The welding current is one of the most important parameters in projection welding. It determines the amount of electrical energy that flows through the workpieces to generate the necessary heat for welding. Too low a current leads to insufficient melting, while too high a current can result in overheating and potential material damage.
2. Welding Time
The welding time is the duration for which the electric current flows through the workpieces. It influences how long the material is heated and, therefore, the size and quality of the weld seam. A welding time that is too short can lead to insufficient fusion, while a welding time that is too long can overheat the material and weaken the joint.
3. Electrode force
The electrode force is the pressure that the electrodes exert on the workpieces. It plays a decisive role in the formation of the weld seam, as it influences the contact resistance between the workpieces. Too little electrode force can lead to insufficient contact and, thus, to a weak weld seam, while too much force can deform the material or wear the electrodes prematurely.
4. Electrode geometry
The shape and size of the electrodes influence the distribution of electrical current and heat to the workpieces. The geometry of the electrodes must be selected to ensure that they make optimum contact with the projection and distribute the heat evenly, ensuring a high-quality welded joint.
5. Material properties of the workpieces
The material properties of the workpieces, such as conductivity, hardness and thermal conductivity, have a significant influence on the welding process. Different materials require different settings for current, time and pressure in order to achieve optimum results. For example, steel requires different parameters than aluminum or stainless steel.
6. Projection height and shape
The height and shape of the projections on the workpiece are decisive for the concentration of the welding current and the formation of the weld seam. Precise control of the projection height and shape is necessary to ensure consistent weld quality.
7. Cooling the electrodes
Cooling the electrodes is important to prevent overheating and extend their service life. Effective cooling ensures that the electrodes retain their shape and function, guaranteeing consistent welded joints.
8. Contact pressure of the workpieces
The contact pressure with which the workpieces are held together before the welding process begins influences the positioning and contact between the projections and the electrodes. Optimum contact pressure is necessary to ensure that the workpieces are held together firmly enough to achieve a high-quality welded joint.
9. Repeatability
Repeatability is a measure of the consistency of the welding process over many cycles. This parameter is particularly important in series production, where consistent quality is required across many parts. Factors such as the stability of welding current, consistency of electrode force, and precise control of welding time contribute to repeatability.
10. Surface finish of the workpieces
The surface condition of the workpieces to be welded influences the contact resistance and, thus, the welding quality. Clean and smooth surfaces ensure good electrical contact and even heat distribution, while dirty or oxidized surfaces can result in uneven welded joints.
Advantages of Projection Welding
High strength
The targeted welding on the projections creates connections that are very strong and durable.
Efficiency
Several welding points can be set simultaneously, which makes the process particularly time-saving and cost-efficient
Precision
The exact placement of the welding points ensures high precision and is particularly suitable for complex components.
Little reworking
As the heating only takes place at certain points, the surrounding material is subjected to minimal stress, which reduces the need for reworking.
The Machines for Projection Welding
Machines for projection welding vary depending on the area of application and the specific requirements of the workpieces. Nevertheless, there are some general features and components that are typical of projection welding machines.
Main components of a projection welding machine
1. Casic construction
As a rule, projection welding machines have a robust steel frame that ensures stability and durability. This frame construction can be either vertical or horizontal, depending on the type of workpieces to be welded. The frame supports the main components of the machine, such as the electrodes, the welding head, the control unit, and sometimes a conveyor belt system.
2. Welding head and electrodes
The welding head is the heart of the projection welding machine. It consists of two main components: the upper and lower electrodes. These electrodes are usually made of copper or a copper alloy, as this material has high electrical conductivity. The electrodes are typically water-cooled to prevent overheating and extend their service life. The welding head can be movable or fixed, depending on the machine.
3. Welding control unit
The welding control unit is the “brain” of the projection welding machine. All important parameters, such as welding current, welding time, and electrode force, are set and monitored here. Modern welding control units are often computerized and offer high precision and repeat accuracy. They can also be equipped with sensors that monitor the welding process in real time and make adjustments if necessary.
4. Pressure mechanism
The pressure mechanism ensures that the electrodes apply the correct force to the workpieces. This mechanism can be pneumatic, hydraulic, or electric motor-driven. Pneumatic systems use compressed air to press the electrodes onto the workpiece, while hydraulic systems offer even greater precision and consistency but are more complex to maintain.
5. Cooling system
Projection welding machines are often equipped with a cooling system that typically uses water to cool the electrodes and other heat-sensitive components. This system is critical to preventing overheating, which could affect the quality of the welds and the lifespan of the machine.
6. Workpiece holders and positioning systems
Depending on the application, projection welding machines can be equipped with special workpiece holders or positioning systems. These ensure that the workpieces are held in the correct position during the welding process. In automated production lines, these holders are often part of a conveyor system that automatically transports the workpieces to the welding station.
7. Conveyor system
In many industrial applications, especially in mass production, projection welding machines are integrated into automated production lines. Conveyor systems are used to transport the workpieces to the welding heads and convey them further after welding. These systems can be based on conveyor belts, rails, or robots.
8. Control panel and user interface
Modern projection welding machines have a control panel with a user-friendly interface. This panel allows operators to control the machine, set parameters, and monitor the welding process. In more advanced systems, the panel can also be connected to a computer that enables additional functions, such as data recording and process analysis.
9. Safety devices
Safety devices, such as safety guards, emergency stop switches, and light curtains, are also an integral part of projection welding machines. These devices ensure the safety of the operator and help prevent accidents during operation.
Discover our expertise in projection welding
Take advantage of precision and efficiency - find out more about projection welding systems from Gatzsch Schweisstechnik and how it can optimize your production! Find out now and take your connections to the next level!
Frequently asked questions (FAQs) about projection welding
Projection welding is a resistance welding process in which two metal parts are joined together under pressure by heating at raised points (projections). These projections concentrate the current flow onto a small area, creating the welded joint.
Projection welding is mainly used for steel, galvanized steel and other conductive metals. It is particularly suitable for sheet metal joints in the automotive and metalworking industries.
In projection welding, pre-formed protrusions (projections) on a metal part are pressed together with another metal part under pressure. An electric current flow through the projections generates sufficient heat to melt the material locally and create a joint.
Projection welding is often used in the automotive industry for fastening nuts, bolts or other attachments to body panels. It is also widely used in electronics and household appliance production.
- High process reliability and reproducibility
- Good electrical and mechanical properties of the welded joint
- No additional material (such as welding rod) required
- Fast process, ideal for series production
In spot welding, the current is conducted directly through the contact surfaces of the workpieces, while in projection welding, pre-formed projections concentrate the current flow on specific points to create the joint there.
The welding current is crucial to generate the necessary heat to melt the metal at the projections. Precise control of the current is important to ensure a clean weld joint without overheating or underheating.
Yes, projection welding is ideal for automation, especially in mass production, e.g. in the automotive industry. Robots and specialized machines can carry out the process very efficiently.
We would be happy to advise you in detail on this topic and support you with the implementation. Contact us for a non-binding inquiry!
The workpiece must be clean and free from contamination such as grease, oil or oxidation. In addition, the projections must be precisely shaped to ensure uniform current distribution and welding quality.
In contrast to processes such as spot welding or roller seam welding, projection welding concentrates the welding current specifically on pre-formed projections. These projections create defined welding spots, making the process ideal for fastening components such as nuts or bolts. It requires less energy than spot welding, as the contact surface is smaller due to the projections.