Hot Riveting: Fundamentals, Advantages, and Applications
Fundamentals of Hot Riveting
Hot riveting is a joining process in which rivets are heated and then plastically deformed to create a secure connection. This method is primarily used when exceptionally high strength and durability are required, such as in the manufacturing of aircraft or in the automotive industry.
In hot riveting, the rivet pin is first heated to a temperature below its melting point but high enough to allow the material to become plastically deformable. The heated rivet is then inserted into a pre-drilled hole in the workpiece and deformed through a pressing motion, creating a firm bond with the workpiece.
Heating the rivet makes the material softer and easier to deform, which allows for a uniform and tight connection. As the material cools, it contracts, further tightening the joint and achieving very high strength.
Hot riveting is particularly used in applications requiring a combination of high mechanical load-bearing capacity and temperature resistance.
System Integration
In modern production lines, hot riveting can be seamlessly integrated into automated processes. Robots and CNC-controlled machines handle the placement and forming of the rivets, ensuring consistent reproducibility and maximum efficiency. Gatzsch Schweißtechnik GmbH offers tailored systems that can be perfectly integrated into your existing production setup.
Experience how our innovative solutions can optimize your production processes. Contact us today for a no-obligation consultation and discover the advantages of our state-of-the-art hot riveting technology for your manufacturing!
Advantages of Hot Riveting
Hot riveting offers several key advantages:
Maximum Strength
Heating the rivet ensures it perfectly conforms to the surrounding material, resulting in an exceptionally strong bond. This strength is ideal for applications subjected to high stress.
Improved Formability
The heat treatment reduces internal stresses in the material, promoting the longevity of the connection and enhancing the quality of the joint.
Durability
Hot-riveted joints are extremely durable, as the precisely controlled heating and cooling make them less susceptible to material fatigue and failure.
Versatility
Hot riveting is suitable for a wide range of materials and thicknesses, making it applicable in various industrial applications.
Hot Riveting in Practice
Hot riveting is used in numerous industries, especially where high demands are placed on the strength and durability of connections. Typical application areas include:
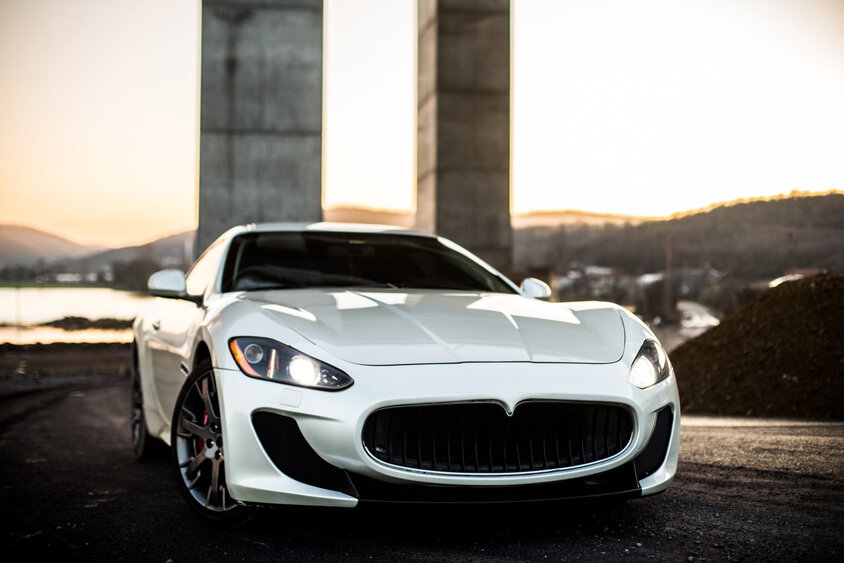
Automotive Industry
Hot riveting is used here to join body panels, chassis components, and other safety-critical parts.
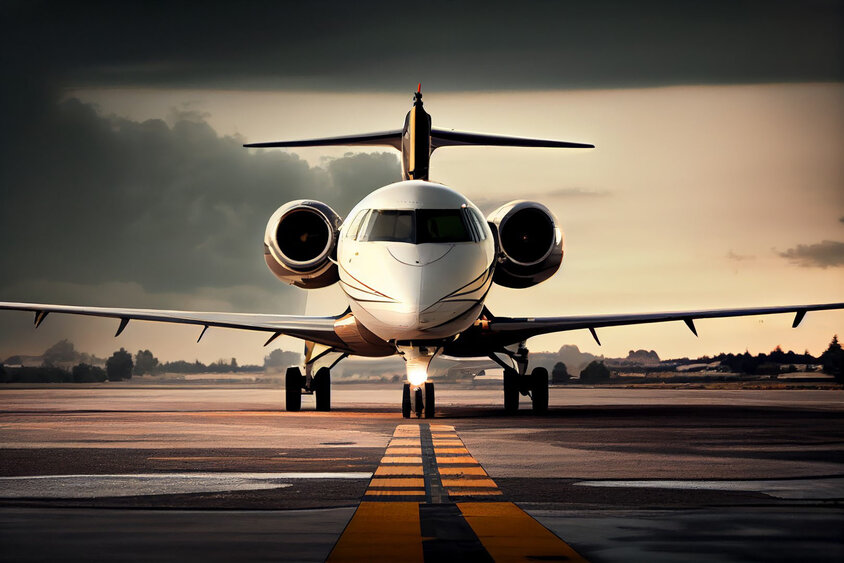
Aerospace
Due to the extreme demands for reliability and strength, hot-riveted joints are frequently used in aviation.
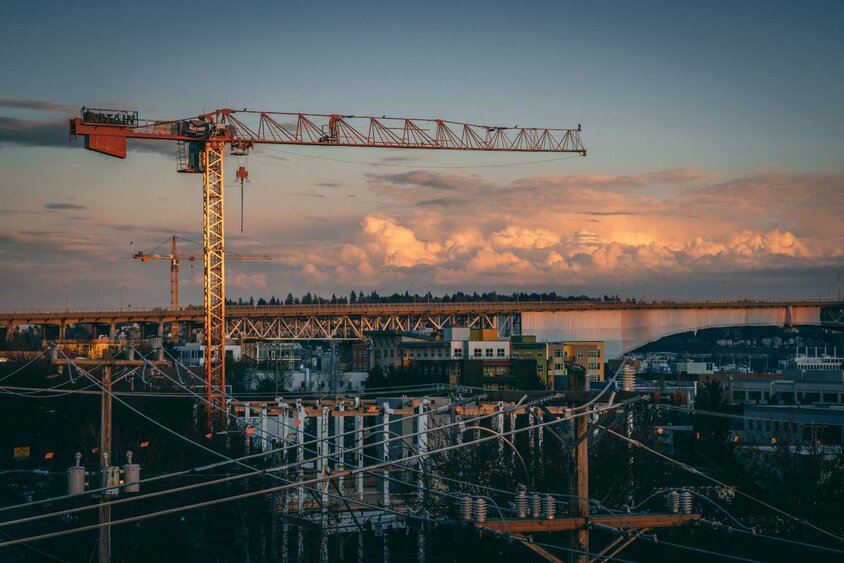
Heavy Industry
Machine and plant engineering, shipbuilding, and the production of large components for energy and infrastructure construction utilize hot riveting for high-load connections.
Key Technical Aspects of Hot Riveting
Material Selection
Choosing the right material for the rivet is crucial. Alloys that exhibit good formability at elevated temperatures and provide high strength once cooled are often used. Common materials for hot riveting include high-carbon steels, specific aluminum alloys, and sometimes copper.
Heating Methods
There are various methods to heat the rivets to the required temperature:
- Induction Heating: This method quickly and uniformly heats the rivet through electromagnetic induction. It is very efficient and precise.
- Gas Flame: A traditional but less precise approach where the rivet is heated directly with a flame.
- Oven Treatment: Rivets are heated in an oven to the desired temperature. This method is suitable for series production as it can process multiple rivets simultaneously.
Temperature Control
Precise temperature control is essential to achieve the desired properties of the joint. Typical temperatures range between 600°C and 1000°C, depending on the material. The temperature affects the flowability of the material and, consequently, the quality of the joint.
Cooling Process
The cooling process can influence the properties of the joint. Controlled cooling can enhance mechanical properties such as hardness and strength. In some cases, the rivet is quenched after setting and forming to further increase its strength.
Specific Characteristics of Hot Riveting
A distinctive feature of hot riveting is the need for precise temperature control. The rivets must be heated to an exact temperature to achieve the desired material properties. Excessive temperatures can make the material brittle, while insufficient temperatures may not achieve the required plasticity.
Frequently Asked Questions (FAQs) About Hot Riveting
Hot riveting is a process used to join components, where rivets are made malleable through heating and then firmly pressed into a borehole. As the rivet cools, it contracts, creating a strong and durable connection.
Hot riveting provides exceptionally high strength and reliability in the joint, even under extreme stresses. It is particularly suitable for applications where resistance to vibration and thermal stability are crucial.
Hot riveting is commonly used with metals, particularly steel, aluminum, and alloys. The choice of material depends on specific requirements for strength, temperature resistance, and corrosion protection.
In hot riveting, the rivet is heated to make it malleable and then pressed into the prepared borehole. As the rivet cools, it contracts and forms a tight, strong connection. The process requires precise temperature control and can be carried out either manually or through automation.
Hot riveting requires specialized equipment that offers precise temperature control and high pressing forces. These machines are often customized to meet the specific requirements of each application.
We are happy to provide you with detailed advice on this topic and support you in the implementation. Contact us for a non-binding inquiry!
Hot riveting processes are subject to strict quality standards, especially in safety-critical industries such as aerospace and automotive manufacturing. Each component is often individually inspected to ensure that the joint meets the required standards for strength and durability.
The correct temperature is crucial for the hot riveting process. Temperatures that are too low prevent sufficient deformation of the rivet, while excessively high temperatures can weaken the material or cause unwanted deformation. Therefore, precise temperature control is essential.
Yes, hot riveting can be fully automated. Modern systems are equipped with sensors and control systems that monitor and optimize the process. This ensures consistently high quality and productivity, especially in series production.
We would be happy to provide you with detailed advice on this topic and support you in the implementation. Contact us for a non-binding inquiry!