Clinching - Technical explanation and application
What is Clinching?
Clinching is a mechanical joining process that enables two or more sheets to be permanently joined together by plastic deformation - without the use of additional joining elements such as screws, rivets or adhesives. The process is particularly effective and is ideal for applications where a stable and invisible connection is required.
Technical details of the clinching process
During clinching, the material of the sheet metal parts is plastically deformed by a punch and a die and thus joined together. The process can be divided into the following steps:
- Preparation: The sheets are placed on top of each other and positioned in a die so that they remain fixed during the process.
- Forming: A punch exerts pressure on the sheets and presses the upper sheet into the sheet below. The pressure creates a localized plastic deformation that presses the material into the die.
- Connection: The punch deforms the material so that it is displaced laterally into the die. This creates a thickening at the joint, which ensures a firm hold between the sheet metal parts. The resulting clinch point is mechanically stable and resilient.
Advantages of Clinching
Clinching has numerous advantages that make it a popular joining process in the industry:
No additional connecting elements
As no screws, rivets or adhesives are required, the process saves material and reduces costs.
Heat-free
In contrast to welding processes, the microstructure of the materials remains unchanged as no heat is applied. This also preserves the corrosion resistance of the materials
Automatability
Clinching processes can be perfectly integrated into highly automated production lines. This enables fast and cost-efficient series production.
Eco-friendly
As neither fumes nor toxic vapors are produced and no additional materials are used, the process is very environmentally friendly.
Another important advantage is the ability to join materials with different properties, such as different material thicknesses or types.
Fields of application of clinching
Clinching is used in many industrial sectors, especially those that place high demands on mechanical stability and precision. The most important areas of application include
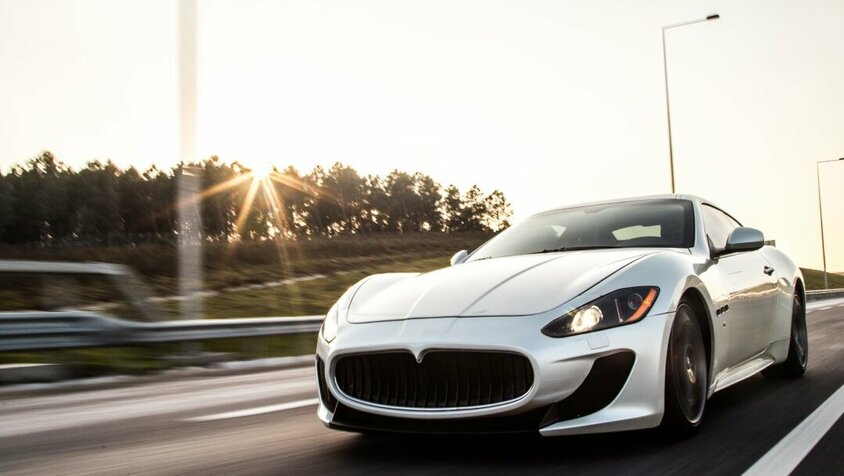
Automotive Industry
Clinching is often used to join car body parts where different sheet thicknesses and materials, such as aluminum and steel, need to be joined together. By using this process, aesthetic, invisible joints can be created that can also withstand high mechanical loads.
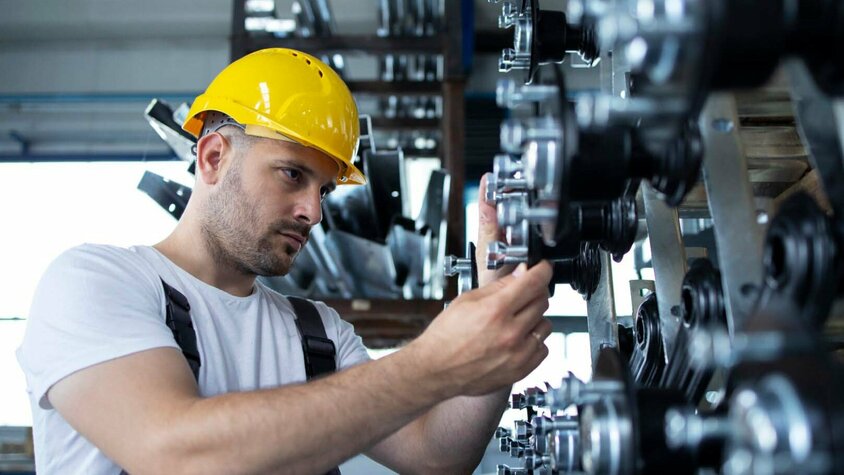
Mechanical Engineering
In mechanical engineering, clinching is used in the manufacture of housings and other components that need to be robust and cost-effective at the same time.
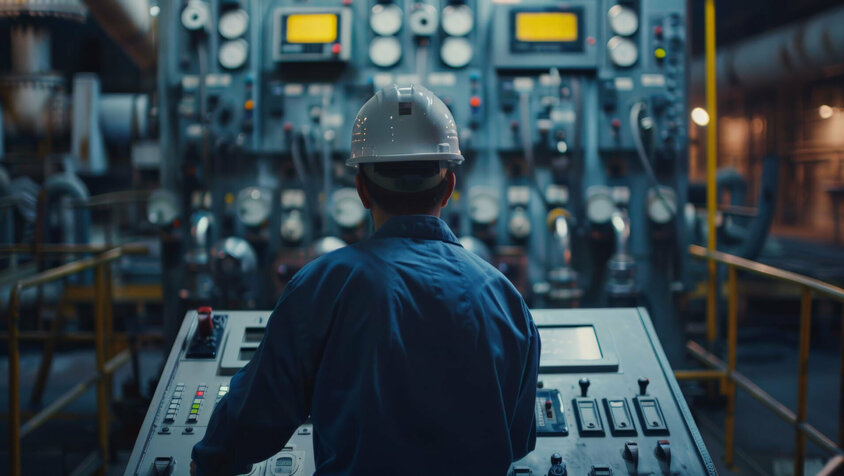
Electrical Engineering
In electrical engineering, clinching is used to join sheet metal and other components for housings, brackets and switchgear.
FAQs on the subject of clinching
Clinching is a joining process in which metal sheets are joined together by plastic deformation without the need for additional joining elements such as screws or rivets.
In principle, many materials can be clinched together, including steel, aluminum, copper and their alloys. Clinching is particularly suitable for joining materials of different thicknesses and properties.
Yes, the connection created by clinching is mechanically stable and durable. It is designed for high mechanical loads and is used in the automotive industry in particular.
The advantage of clinching is that no heat is used, which means that the material properties remain unaffected. It is also more environmentally friendly, as no fumes or toxic vapors are produced. Furthermore, no additional materials such as welding rod are required.
Yes, the clinching process can be perfectly integrated into automated production lines, enabling fast and cost-efficient production.
We are happy to provide support.
Clinching works particularly well with thin to medium-thick sheets. In practice, the material thickness is usually between 0.5 mm and 3 mm. However, depending on the specific application and the technique used, thicker materials can also be joined together.
Limitations may occur if extremely thick materials or sheets with high hardness are to be processed. In such cases, a thorough check of the material combination is necessary.
Yes, clinching can be used on coated materials without damaging the coating. This preserves the corrosion protection of the materials, which is particularly important for galvanized steel or painted surfaces.
The load-bearing capacity of clinch connections depends on various factors, such as the type and thickness of the material and the tool used. As a rule, however, clinch connections are highly resilient and are suitable for applications in which both tensile and shear forces occur.
Clinch connections are form-fit and permanent connections that cannot be released non-destructively. However, if necessary, the connection can be mechanically broken or the component replaced with a new connection.
Clinching is mainly suitable for flat sheet metal parts or components with slight curvature. For complex geometries or strongly shaped components, the use of clinching may be limited. In such cases, adjustments to the process design or alternative joining methods are required.
Special clinching machines equipped with a punch and die are used for clinching. These machines can be operated manually, semi-automatically or fully automatically, depending on the application requirements.
We will be happy to advise you.
Clinching does not use any additional material such as rivets or screws, which makes it more cost-efficient. In addition, the joint remains invisible as there are no external fasteners. Compared to welding, no heat is used, which means that the material properties remain unchanged.
Yes, clinching is particularly suitable for series production as it can be easily automated. The process is fast and can be carried out in large quantities with consistent quality.
There are various clinching processes, such as conventional clinching, full-punch clinching and half-punch clinching. The differences lie in the way in which the material is formed and whether the material is completely or partially cut through. The appropriate process can be selected depending on the application.
In most cases, no reworking is required as clinching produces a clean, positive connection. However, if a particularly smooth surface is required, minor adjustments or surface treatments can be carried out after clinching.
Yes, clinching can be combined with other joining processes, such as welding or gluing. In the automotive industry, it is often used with other techniques to ensure maximum stability and durability.