Spot welding: A comprehensive introduction to the technology and application
Technical basics and applications of spot welding
Spot welding is a widely used process in manufacturing that joins metal parts quickly and precisely by applying heat and pressure at specific points. As an efficient method of resistance welding, it is utilized in many industries, such as automotive production and mechanical engineering. This process offers a reliable and economical way to produce stable and durable joints, making it an indispensable part of modern production techniques.
What is spot welding?
Spot welding is a welding process in which two metal parts are joined together at specific points through the targeted application of heat and pressure. It belongs to the category of resistance welding, where the electrical resistance of the workpieces is used to generate heat through the flowing current, leading to the melting and joining of the metals.
As your partner for spot welding, we offer customized welding guns and machines. Whether for new developments, modular systems, or customized standard solutions, we manufacture precisely according to your requirements.
How does spot welding work?
The process sequence
In spot welding, two electrodes are applied to the metal parts to be joined. A strong electric current flows through the electrodes, heating the metal parts at the contact points to such an extent that they melt. At the same time, pressure is applied to the parts, causing them to fuse firmly together at the heated points. As soon as the current is switched off and the material cools down, a permanent bond is created. The process essentially consists of three phases:
-
Application of force: At the beginning of the process, the metal parts to be joined are placed between two electrodes. These electrodes are usually made of copper, which has high electrical conductivity and heat resistance. The electrodes press the workpieces together with a defined force, creating a firm contact between the surfaces to be joined.
-
Current flow and heat generation: After the electrodes have fixed the workpieces in place, an electric current is passed through the electrodes and the workpieces. The resistance of the metals to the current generates heat at the contact points. This heat causes the metals to melt locally and join together in a so-called “welding spot”.
-
Cooling and hardening: As soon as the welding spot has been formed, the current is switched off. However, the electrodes remain on the workpieces for a short time to allow the joint to cool under pressure. During this cooling process, the molten metal solidifies and forms a strong, permanent joint.
Welding parameters
The quality and strength of the welded joint depends on various parameters:
-
Amperage: A higher current generates more heat, which is necessary for thick materials. With thinner materials, however, too high a current can lead to overheating and a weak joint.
-
Welding time: The duration of the current flow influences the size of the weld spot. A welding time that is too short can lead to an inadequate joint, while a time that is too long can result in material damage.
-
Electrode force: The contact pressure of the electrodes must be high enough to ensure good contact, but not so high that the material is deformed or damaged.
-
Electrode shape: The shape and size of the electrodes influence the distribution of heat and therefore the size and shape of the welding spot.
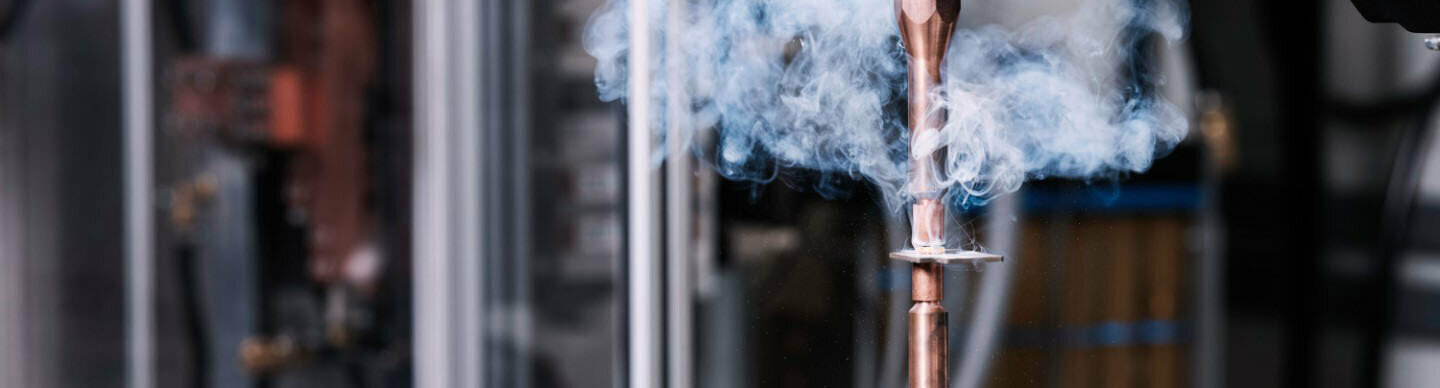
Advantages of Spot Welding
Efficiency and speed
One of the biggest advantages of spot welding is its efficiency. The process is fast and can be easily automated, making it ideal for mass production. The ability to make many spot welds in a short time reduces production costs and increases the throughput rate.
Economic efficiency
Spot welding is economical as it does not require filler materials such as welding wire or flux. Material consumption is low, and as the process can be automated, labor costs are relatively low. In addition, the process does not require extensive post-processing as the spot welds often remain invisible.
Quality of the joints
Spot welding produces strong, durable joints that are both mechanically and thermally resilient. The spot welding minimizes distortion of the workpieces and results in a clean, aesthetically pleasing joint.
Clean and environmentally friendly
As no additives are used in spot welding and the process produces little smoke or fumes, it is a clean method that can also be used in sensitive environments. This helps to reduce environmental pollution and improves working conditions.
Suitable materials for spot welding and their special features
Spot welding is particularly suitable for materials with good electrical conductivity and a relatively low melting temperature. Frequently used materials are:
Steel
Steel, especially low-carbon steel, is the most commonly used material for spot welding. The low carbon content reduces the risk of cracks and makes the material easy to weld. Spot welding is often used in the automotive industry to join steel body parts.
Stainless steel
Stainless steel is a popular material in many applications due to its corrosion resistance. However, when spot welding stainless steel, special electrodes must be used to prevent the formation of oxides and discoloration. Stainless steel requires precise control of the welding parameters as the material has a higher melting temperature than conventional steel.
Aluminum
Aluminum is an important material due to its lightness and corrosion resistance, but poses particular challenges in spot welding. Due to aluminum's high thermal conductivity, the current must be precisely controlled to ensure a consistent welded joint. Aluminum also tends to form oxides on the surface, which can affect the weld quality. Careful surface preparation is therefore required.
Application of spot welding
Spot welding is used in many industries, especially where fast, efficient and automated joining of metal parts is required:
Automotive industry
In the automotive industry, spot welding is the preferred method for joining body and structural parts. The ability to join metal parts quickly and reliably makes it ideal for the mass production of vehicles. The automation of spot welding makes it possible to make hundreds of spot welds per vehicle in a short time, which significantly increases production speed.
Aerospace industry
In the aerospace industry, spot welding is used to join aluminum and titanium components. These materials are lightweight but strong, making them ideal for aircraft structures. The ability to produce strong and precise joints is particularly important in this industry to meet safety standards.
Challenges and limits of spot welding
Despite the many advantages, there are also some challenges:
Limited material thickness
Spot welding is particularly suitable for thin sheets. With thick workpieces, it can be difficult to generate the required heat through the entire material. This limits the application range of the process.
Surface quality
The quality of the welded joint can be influenced by the surface finish of the workpieces. Painted or coated surfaces can impede the flow of current and lead to weak joints. Careful surface preparation is therefore often necessary.
Welding of aluminum
Welding of aluminum requires special care. Due to its high thermal conductivity and tendency to form oxides, precise control of the welding parameters is necessary to ensure a high-quality joint.
Our solutions for your requirements in spot welding
At Gatzsch Schweißtechnik, we develop and manufacture spot welding machines and systems that are perfectly tailored to your individual requirements. Whether you need a standard machine or a customized solution - we offer you the right technology for reliable and durable welded joints. Discover our extensive product range and let our experts advise you.
The most important FAQs on the subject of spot welding
Spot welding is a welding process in which two metal sheets are joined together by creating spot welds. These spot welds are created by electrical resistance and high pressure.
In spot welding, a high electric current is passed through two electrodes that press on the metal. The electrical resistance between the two metal parts generates heat, which melts and joins the metals at the points of contact.
Typically, metals such as steel and stainless steel are used for spot welding. Aluminum and other non-ferrous metals can also be spot-welded, but require specific adjustments.
The process is fast, cost-efficient and ideal for series production. It requires no additives such as welding rod and leaves a clean, minimally visible seam.
Spot welding is particularly widespread in the automotive industry, where it is used to join car body parts. However, it is also used in the electronics and household appliance industries.
The strength of the spot welds depends on factors such as material thickness, welding parameters and electrode quality. Well-made spot welds are very stable and meet high safety requirements.
Special spot welding machines are used for spot welding, which are usually fully automatic in industry. However, there are also smaller, manual devices for workshop use.
Yes, it is possible to join different metals, but this requires precise adjustment of the welding parameters, as each material has different electrical resistance values and melting points.
To extend the service life of the electrodes during spot welding, regular cleaning of the electrodes is crucial to ensure a clean contact surface. Selecting the right material for the electrodes is also important, as it must be matched to the material to be welded and the area of application. In addition, the welding parameters, such as amperage, welding time and electrode force, should be optimally adapted to the respective material. Precise adjustment of these parameters reduces wear and ensures an even load on the electrodes, which significantly increases their service life.
The welding quality can be tested using non-destructive testing methods such as ultrasonic tests or tensile tests. Regular maintenance and calibration of the welding machines are also essential.