Basics of Arc Welding
Arc welding is one of the most commonly used welding processes in metalworking and processing. It is characterized by its versatility and efficiency, which is why it is widely used in many branches of industry, including the automotive industry, mechanical engineering and the construction industry.
What is arc welding?
Arc welding is a welding process in which an electric arc is used as a heat source to melt and join metals. It is one of the most commonly used welding methods in metal processing and is used in many industries, such as the automotive industry, mechanical engineering and construction. The arc is created between an electrode and the workpiece and generates temperatures of over 3000 degrees Celsius, which are sufficient to melt the metal at the welding point and create a permanent bond.
What types of arc welding are there?
There are different types of arc welding that offer different advantages depending on the application and material. The main difference is whether the electrode melts during welding or not.
Welding processes with melting electrodes
Metal Shielded Gas Welding (MIG/MAG) (MIG/MAG)
In this process, a wire is continuously fed as an electrode while a shielding gas surrounds the arc to protect the weld seam from atmospheric influences. MIG stands for Metal Inert Gas welding and is mostly used for non-ferrous metals, while MAG stands for Metal Active Gas welding, which is commonly used for steel.
Manual Arc Welding (Stick Welding)
This is the most traditional and simplest method, using a consumable electrode. It is often used for repairs and smaller welding tasks since it does not require an external gas source.
Submerged Arc Welding (SAW)
This process uses a consumable wire electrode and operates under a layer of flux powder. The powder partially melts and protects the weld seam from atmospheric influences while simultaneously forming slag. It is often used for thick materials and long, straight welds.
Electroslag Welding (ESW)
In electroslag welding, the electrode melts in a slag bath, which is heated by electrical resistance. This method is particularly suitable for welding thick plates and large components in a vertical position.
Stud Welding
In stud welding, a stud is welded to the base material using an arc. The stud melts at the contact point and forms a strong bond with the workpiece. This method is commonly used in steel construction, the production of switch cabinets, and the automotive industry.
Welding Processes with Non-Consumable Electrodes
Tungsten Inert Gas Welding (TIG)
This process uses a non-consumable tungsten electrode. The arc burns between the electrode and the workpiece while an inert gas, often argon, protects the welding area. This method offers precise control and is often used for thin materials or critical applications.
Plasma Welding
Plasma welding is an advanced form of TIG welding, where the arc is constricted through a nozzle to generate plasma. The tungsten electrode does not melt. This process provides a highly concentrated heat input, allowing for precise welds, especially on thin materials and complex geometries.
Submerged Arc Welding (SAW) and Electroslag Welding (ESW) are also classified as processes using consumable electrodes. Both methods are known for their efficiency in handling large workpieces and thick materials. Stud welding can be considered a special process, as it is specifically used for welding studs onto workpieces, using a consumable electrode. Plasma welding, on the other hand, belongs to the non-consumable electrode processes, similar to TIG welding, but offers even greater precision and flexibility due to the use of a plasma beam.
Advantages of Arc Welding
Arc welding offers a powerful, flexible, and cost-effective solution for creating permanent joints in various metalworking industries. With its diverse methods, almost every requirement in industrial manufacturing and craftsmanship can be met. For companies that prioritize quality and efficiency, arc welding is indispensable.
Versatility
Arc welding can be used for a wide range of metals and material thicknesses.
Cost-Efficiency
The equipment for arc welding is often more affordable compared to other welding techniques, and the operating costs are lower.
Fast Welding Process
Arc welding allows for high welding speeds, especially in automated applications.
Strong Weld Joints
Joints produced by arc welding are extremely durable and long-lasting.
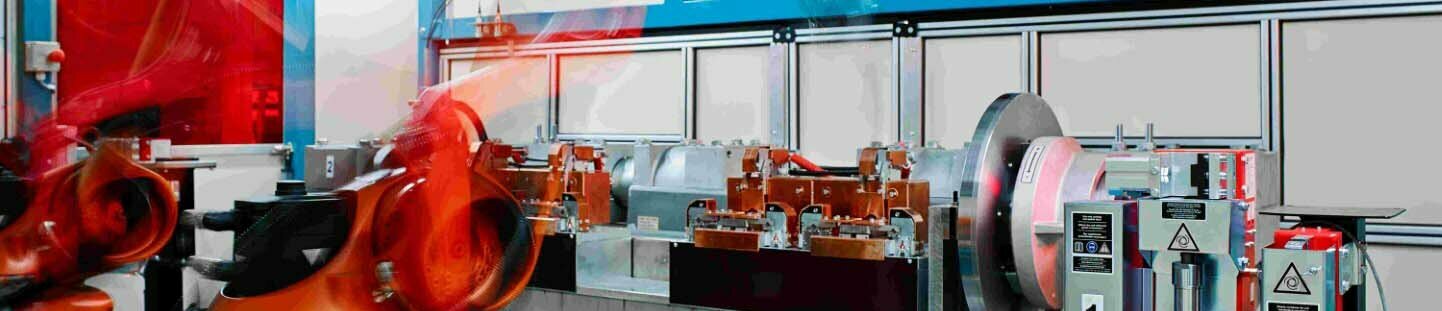
How Does Arc Welding Work?
Arc welding works by generating an electric arc between an electrode (which serves as either the positive or negative pole) and the workpiece to be welded. The arc is created when the circuit is closed, and the electrode makes contact with the workpiece. When the electrode is withdrawn, an electric arc forms, which serves as an intense heat source.
The Process in Detail:
-
Power Supply: A welding power source provides the necessary electric current, which flows through the electrode. Depending on the process, either direct current (DC) or alternating current (AC) can be used.
-
Arc Formation: When the electrode touches the workpiece and is then pulled back, an arc is formed. This arc is a continuous electric discharge that melts the metal at the weld site.
-
Weld Pool: The melted metal forms a weld pool, in which the material of the electrode (if it is a consumable electrode) and the workpiece fuse together.
-
Protection of the Weld Area: Depending on the welding process, the weld pool is shielded from atmospheric elements such as oxygen and nitrogen by shielding gases (like argon or CO2) or by molten flux (as in submerged arc welding). This protection prevents porosity and other welding defects.
-
Solidification: After the welding process, the molten metal solidifies, forming a solid, durable joint between the two workpieces.
-
Post-Processing: In some processes, slag is produced and must be removed after welding. Depending on the requirements, a visual inspection or non-destructive testing (NDT) may be conducted for quality assurance.
Our Expertise in Arc Welding
If you are looking for customized welding solutions that offer the highest quality and efficiency, contact us today.
Our experts at Gatzsch Schweißtechnik are here to discuss your individual requirements and develop the perfect welding system for your projects. Let’s optimize your production together – we look forward to hearing from you!
The Most Important FAQs About Arc Welding
Arc welding is a process that uses an electric arc to melt and join metals. It involves creating an electric arc between an electrode and the workpiece, producing intense heat that melts the metals at the weld joint, forming a strong, durable bond once cooled.
The most common methods are:
- MIG/MAG Welding (Metal Inert Gas/Metal Active Gas Welding)
- TIG Welding (Tungsten Inert Gas Welding)
- Manual Metal Arc Welding (Stick Welding)
- Plasma Welding
Each has specific applications, depending on the material and requirements.
- High welding speed
- Versatile for different materials (steel, stainless steel, aluminum)
- Good control over the weld seam
- Economically efficient for many applications
The choice of electrode or welding wire depends on the materials being welded and the welding process used. Steel requires different electrodes than stainless steel or aluminum. It is important to select the correct filler material to ensure a clean and stable weld seam.
Arc welding is particularly well-suited for metals such as:
- Steel
- Stainless Steel
- Aluminum
- Copper
However, there are specific processes for some materials with special properties, such as high conductivity or corrosion resistance.