Adhesive Bonding – The Smart Solution for Strong Connections
In recent decades, adhesive bonding has emerged as an innovative and versatile method for securely and efficiently joining a wide range of materials. From the automotive industry to electronics and construction, adhesives offer solutions where traditional joining techniques like welding, screwing, or riveting reach their limits. But what makes adhesive bonding so special, and why is it being used more frequently?
What is Adhesive Bonding?
Adhesive bonding is a modern joining technique in which materials are bonded together using adhesives. It differs from traditional mechanical methods like riveting or screwing, and thermal processes like welding. While these methods require strong mechanical forces or high temperatures, adhesive bonding relies on the chemical or physical adhesion of adhesives to the surfaces being joined.
Fundamentals of Adhesive Bonding Technology
Surface Preparation
Proper preparation of the surfaces to be bonded is crucial to ensure optimal adhesion. The surfaces must be clean, dry, and free from contaminants such as grease, dust, or corrosion inhibitors. Often, additional surface treatments like roughening or chemical activation are necessary to improve adhesion.
Adhesive Application
The adhesive is applied to one or both bonding surfaces. Various forms of adhesives can be used, including liquids, pastes, tapes, or films. The choice of adhesive and application method depends on the specific requirements of the application and the material properties.
Joining and Curing
After applying the adhesive, the materials are pressed together to ensure the adhesive is evenly distributed. Depending on the type of adhesive, curing can occur at room temperature, through heating, or with the use of UV light or other energy sources. The curing time varies depending on the adhesive, ranging from a few minutes to several hours, during which the adhesive reaches its final strength.
Adhesive Bonding in Practice
Adhesive bonding is used in many industries and has established itself as a key technology in modern manufacturing. Some typical areas of application include:
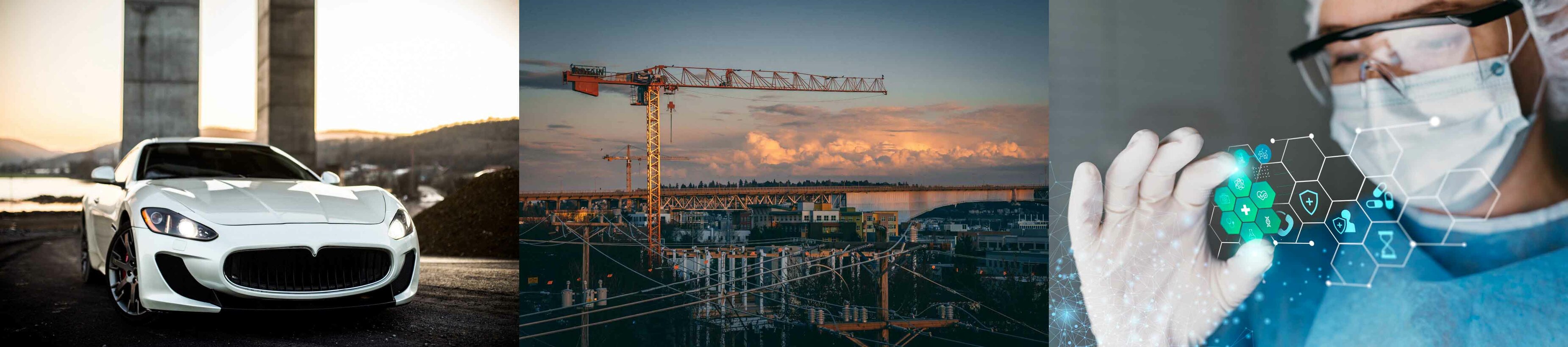
Automotive Industry
In the automotive industry, adhesive bonding is used to join body parts, windshields, and safety-critical components. It plays a crucial role in lightweight construction, as it allows for the bonding of different materials like aluminum, steel, and plastic without the added weight of mechanical fasteners. Additionally, it enhances crash safety and the overall rigidity of the vehicle.
Aerospace
In aerospace, saving weight is critical without compromising structural integrity. Adhesive bonding enables the joining of lightweight but high-performance materials such as fiber-reinforced composites and metals. It also helps reduce vibrations and improves aerodynamic efficiency.
Electronics
The miniaturization of electronics demands solutions that securely bond the smallest components without damaging sensitive parts. Adhesives provide a reliable solution, offering both electrical insulation and mechanical strength.
Medical Technology
In the manufacturing of medical devices, adhesive bonding is used to join components like catheters, syringes, or implants. Biocompatible adhesives play a crucial role here, as they can be safely used within the body.
Construction
In construction, adhesive bonding is used to connect building materials such as glass, concrete, and metal. Adhesives enable invisible, permanent connections between components, contributing to aesthetically pleasing and modern architectural designs.
Advantages of Adhesive Bonding
Material Versatility
Adhesives enable the bonding of a wide range of materials that are difficult or impossible to join using traditional methods.
Even Stress Distribution
Mechanical fasteners like screws concentrate forces at specific points, which can reduce load-bearing capacity. Adhesives evenly distribute the stress across the entire bonding surface.
Lightweight and Flexibility
By eliminating mechanical fasteners, the overall weight can be reduced, which is especially important in the automotive and aerospace industries.
Witterungs-beständigkeit
Viele Klebstoffe sind resistent gegen Feuchtigkeit, Chemikalien und extreme Temperaturen, was sie für Anwendungen im Freien oder in rauen Umgebungen prädestiniert.
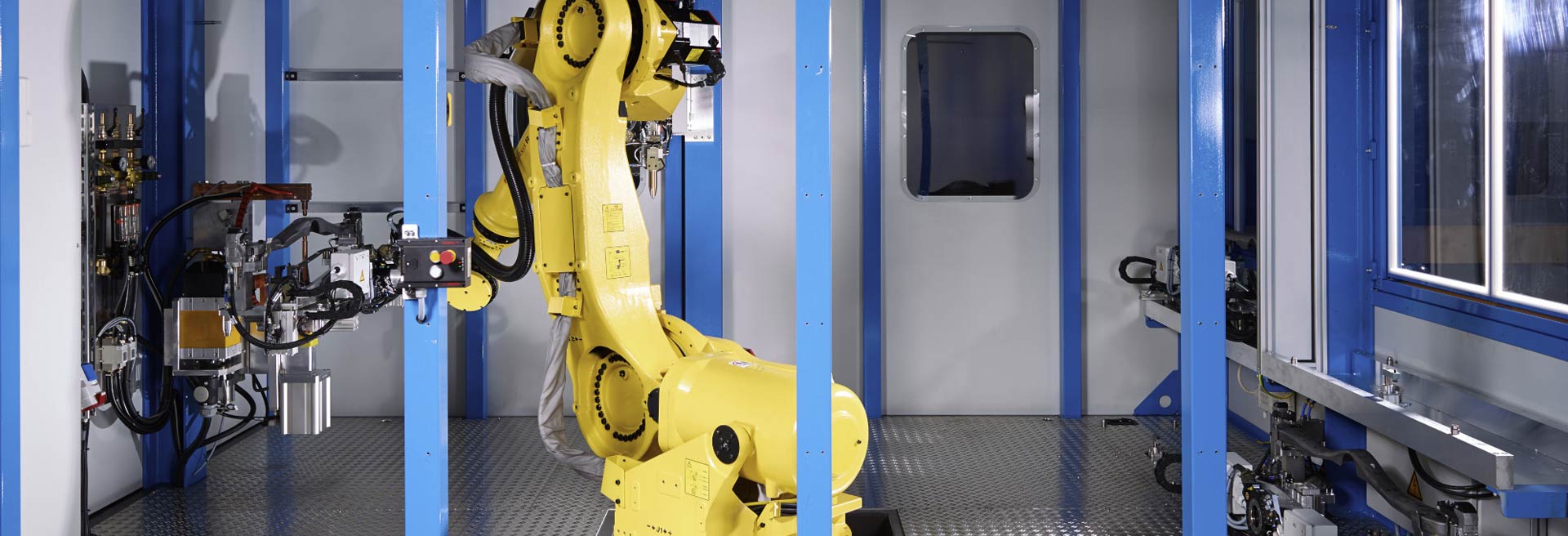
Technical Fundamentals of Adhesive Bonding Technology
Adhesive bonding is based on the principles of adhesion and cohesion. Adhesion refers to the bonding force between the adhesive and the surface of the material being joined, while cohesion is the internal strength of the adhesive itself. Together, these forces ensure that materials are securely and permanently bonded. Depending on the application and requirements, there are different types of adhesives.
Physically Curing Adhesives
These adhesives cure by evaporating solvents or water or by cooling. They offer the advantage of being relatively quick to process and cure at room temperature or through cooling.
Contact Adhesives
Contact adhesives provide immediate bonding and do not require a long curing process. They are ideal for materials that need to be quickly joined, such as plastics and leather.
Hot Melt Adhesives (Hotmelts)
These adhesives are melted at high temperatures and harden upon cooling. They are especially popular in the packaging industry.
Chemically Curing Adhesives
These adhesives cure through a chemical reaction in which two or more components interact to create a strong bond. They offer particularly high strength and durability.
Epoxy Adhesives
Epoxy adhesives are known for their high strength, chemical resistance, and excellent adhesion to various materials such as metal, plastic, and glass. They are ideal for structural bonding in aerospace and construction.
Polyurethane Adhesives
These adhesives offer excellent elasticity and are often used in the construction industry to create seals and flexible connections. They can bond to both porous and smooth surfaces.
Acrylic Adhesives
These adhesives offer fast curing times and high impact resistance. They are ideal for applications that require quick production processes, such as in the electronics or automotive industries.